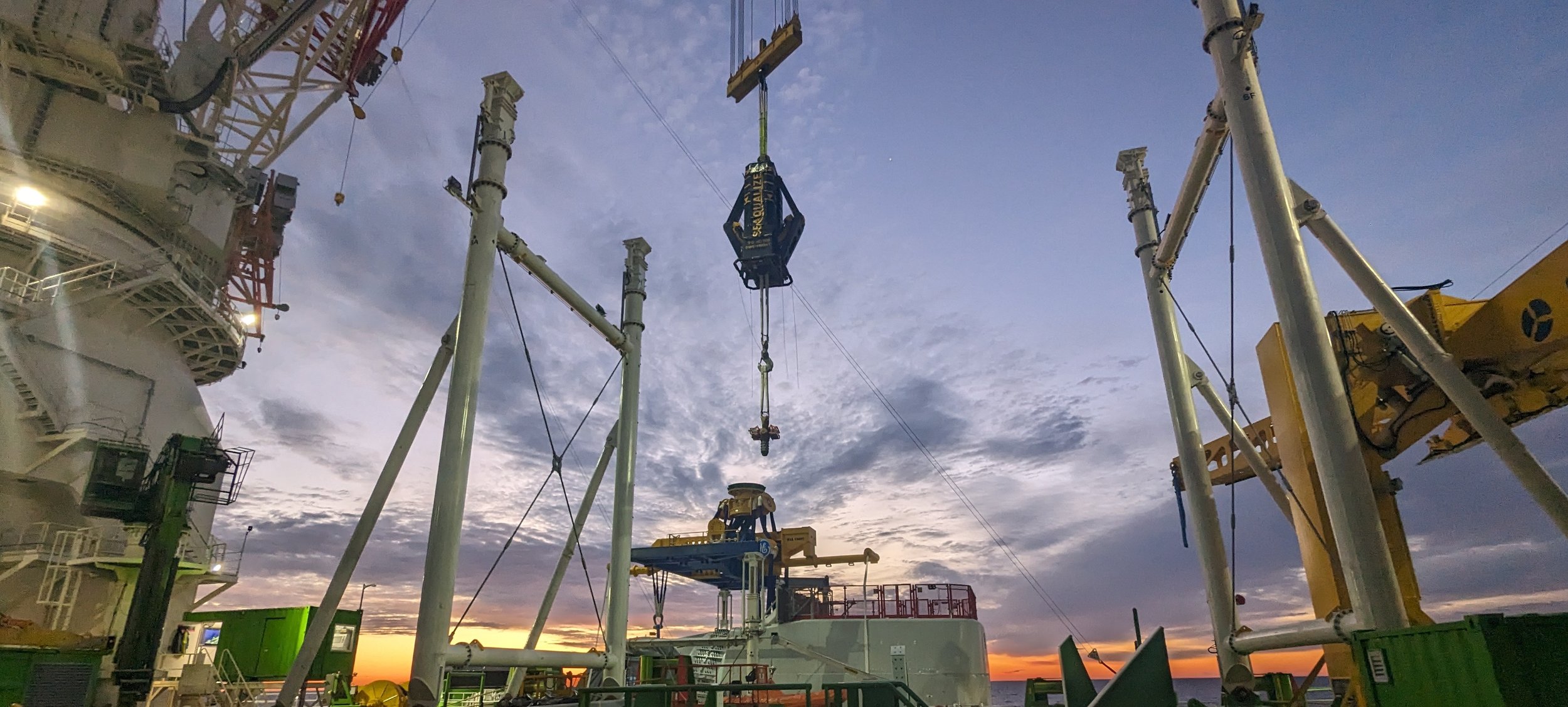
The HeaveChief: Hook based Balanced Heave Compensation
Ranging from ~50 mT to eventually 2.000 mT and beyond, it opens up the road to floating installations of offshore wind turbine components, complete turbines at once! Plus, it improves safety, level of control and speeds up your operation when lifting loads from feeder or supply barges.
The patented Seaqualize technology combines a very strong passive system, keeping the full load ‘weightless’. A small power efficient active system (~5-10%) precisely positions the load, and prevents accidental lift-offs or shock loads.
Our technology allows for heavy weight, in-air heave compensation that offers the reduced velocity and impacts that equipment manufacturers demand while protecting your crane. It turns every standard heavy lift crane into a high-performance AHC crane, only when the job requires. Seaqualize offers flexible lease solutions and operator support.
Why waste power, if you can balance any load?
Workability increase: work in higher seas all year round
Hook based active heave compensation reduces heave motions and set down-velocities by up to 95%. This allows shorter and better plannable installation campaigns:
Less waiting on weather days
Work longer into the heavy weather winter seasons
Faster and safer operations due to increased set-down control
The Seaqualize Delta can offer up to ~20-40% workability increase, especially in the demanding North-Sea.
Would like to analyze the potential workability increase for your operation in a particular location? Reach out to us, and we are more than willing to help using our in-house workability software.
Amount of time [%] at North Sea wind farm (Dogger Bank) when max. set-down speed < 5 cm/s. Workability analysis of 180m heavy lift vessel, crane positioned at stern, hook at 110m height, 30m radius, mass load 500 mT.
Performance benefits of the Seaqualize Delta
Increased control over in-air heavy load
Geostationary load: up to 95% motion reduction results in heavy loads that can be kept virtually motionless during in-air lifts while the crane vessel is subjected to sea states of Hs 2,5 to 3.0
Internal controls: Internal tool actuation controls for precise positioning and monitoring, fully parallel to standard hoist controls
increased control in load set-down phase
Slow set down: Set down velocities of 5 to 7 cm/s while in Hs 3.0 conditions
Accidental lift-off protection: 1,5m free stroke to prevent accidental lift-off under all circumstances
Snag load protection: the Delta tool absorbes any load shocks that may occur during the set-down phase, protecting the crane while increasing it’s load capacity
Increased load handling window: Guarantee longer period during which load is set-down but still ready for quick lift-off
Increase safety in heave compensated operations
No unintended actuation: Small actuation system (10% of full load) is incapable of provoking undesired load motions
Full passive load control: Passive system keeps the load fully balanced and under control for prolonged periods during any major system failure
Continuous, safe operation for lifting loads from feeder barges
Continuous operation: no need to waste critical time by taking the tool back to the deck, for re-charge or to change settings. Keep on lifting cargo from the feeder barge until its empty, regardless of varying loads
Safe handling: tool can adjust to any constant tension setting, for example to check the rigging, and switch to fully passive compensation for longer times when needed
Reduced DAF: tool can gradually introduce weight, keeping DAF < 1.1
Technical specifications
Heave Chief 750 & 1100
The Heave Chief is the first in-line heavy lift heave compensator with Seaqualize BHC technology. It is designed as a fully flexible tool that can be placed in any crane hook, and compensate heave motions up to ~95%. It has internal controls to allow for delicate set-down and pick up of loads.
HC750
SWL: 750 mT
Resulting DAF: < 1.1
Effective tool height under hook: 2.5 m
Absolute tool height: 9.5 m
Speed: 0,5 m/s
Weight: 125 mT
Stroke: 2,5m
Fully electrically powered (battery or umbilical), ~30kW
Usable in every crane hook, no adjustments or additions to crane needed
Mobilization times < 1 day
Certification: DNVGL-0378 Lifting appliance
HC1100
The HC1 100 will be delivered around April 2023 and will have upgraded specifications compared to the HC750. Its design is more focussed on easy feeder barge lifting, facilitating a single lift point at the bottom of the tool. Compared to the HC750, the changed performance specifications are:
SWL: 1100 mT
Weight: 150 mT
Stroke: 3,5 m
Speed: 0,7 m/s
Operations
The Delta is targeting various kinds of offshore operations:
Installing delicate loads onto a fixed platform, using a heaving vessel, for example: the set-down of a wind turbine component on a fixed platform such as a transition piece (TP) onto a monopile (MP) or a nacelle onto a tower. Have a look at the advantages of using inline AHC for floating installations.
The Seaqualize inline AHC tooling, enables safe and continuous active quick-lifting from supply barges. Of key interest for the US offshore wind market but applicable anywhere where additional workability is needed: using the Delta offers on average >80% workability even in the winter months. Have a look at the advantages of using our tooling for feeder barge lifts.
The Delta inline AHC tooling can actively match the motions of a heaving supply vessel, allowing for safe and easy returning of cargo to a supply vessel from a jack-up crane of floating HLV, to free up desk space from equipment or material that is no longer needed. Have a look at the advantages of using the inline AHC for such operations.
We regularly do preliminary operational simulations, or detailed HAZID reviews, with field experts from Heerema Marine Contractors or Van Oord Offshore Wind, such as superintendents and crane drivers. Based on their feedback, we are improving feedback interfaces, tool controls, operational functionality or simply how to rig the tool.
We perform additional operational tests in-house to verify how our functionality holds up in various cases. For example: how to balance a turbine blade including the lifting tool that needs to stay behind?
Prototyping timeline
2018 - Delta 0.05
Concept testing explaining the principle of the Delta heave compensation technology
2019 - Delta 2
Subsystem prototype: testing all final subsystems on scale.
Interested in prototype test results? Have a look here!
2020 - Delta 600
Start with engineering, production, certification and testing of the first full-scale demonstrator. commissioning starts February 2021, Offshore demonstrations possible from June 2021 onwards. Off-shore tests with Van Oord Offshore Wind planned October 2021. Project partners include Van Oord, MARIN and TNO.
The development of the Delta600 is supported by the Dutch ministry of Economic Affairs, through a Renewable Energy subsidy
2020: Delta2 tests
We test regularly with our Delta2 prototype, to try out new software or hardware. This time we wanted to use a different load than normally…
Have a look at other Delta2 test registrations